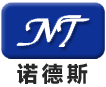

(1) According to the process, it is divided into wet pressing, dry pressing, and semi dry (wet) pressing.
A. Wet pressing refers to the rapid extrusion drying of pulp by immediately transferring it to mold molding (in mold drying) after wet embryo molding.
Advantages: This process has high production efficiency, can be transferred to molding immediately after molding, and has fast production speed; The moisture content of the wet embryo during the wet pressing process is about 65-75%, which is high and requires a longer vacuum adsorption time. The surface of products produced by wet pressing process is smooth, delicate, and beautiful. Wet pressing products have thinner wall thickness, higher density, and save volume.
Disadvantages: Products with small inclination are not easy to stretch or demould; Products with smaller angles or slopes have higher net crushing rates. It consumes a lot of heat energy.
Main product types and application fields of wet press pulp molding: electronic products are lined with industrial packaging (such as Dell computer box, mobile phone liner box, razor box), various tableware, masks, decorative wall panels, etc., mostly used in areas with high added value.
B. Dry pressing refers to using air drying, basket drying, natural drying, or special drying equipment such as sunlight room, wind power, vacuum, etc. to dry and then reshape.
Advantages: Low cost, high efficiency, and good buffer performance.
Disadvantages: The surface sensory quality is relatively rough, and the adaptability of post processing such as printing is poor.
Application fields of dry press pulp molded products: industrial buffered packaging, egg tray, egg box, seedling tray, seedling tray, fruit tray, and so on.
C. Semi dry (wet) pressing refers to drying the wet embryo of pulp molding, using special equipment to regain moisture to a moisture content of 25% to 45%, and then using thermal molding for shaping.
Advantages: The quality of the finished product is between dry pressing and wet pressing, but the efficiency is greatly improved.
Disadvantages: Average surface quality, not suitable for post printing processing.
Application field: outer packaging for gifts and daily necessities with low requirements, and inner buffer packaging with relatively high requirements.
(2) Pulp molding is divided into:
Boutique work package (such as full pulp molded electronic product packaging, cosmetics packaging, wine packaging, cigarette packaging, etc.);
Ordinary work package (such as buffer lining);
Food packaging (tableware, cake trays, dumpling plates, packaging boxes, etc.);
Packaging of agricultural products (flower pots, nursery cups, seedling trays, sand fixation trays, fruit trays, etc.);
Medical packaging (urinal, kidney shaped tray, medical urinal, medical needle box, vaccine holder, pregnancy test stick, etc.);
Building materials (decorative wall panels, etc.);
Pet supplies (cat litter tray, cat and dog food tray, cat house, etc.);
Furniture supplies (stools, storage boxes, ice buckets, clocks, barbecue boxes, etc.);
Cultural and creative daily necessities (pulp molded masks, hats, slippers, masks, toys, etc.);
Pulp molded containers (wine bottles, beverage bottles, etc.);
Others (sprue pipes, parts, balloon holders, toys, etc.)
(3) Pulp molding by raw material:
Recycled pulp products (yellow pulp, newspaper pulp, etc.), sugarcane pulp products, wheat straw pulp (straw) products, bamboo pulp products, wood pulp products, reed pulp products, palm pulp products, melon and rattan pulp products, cotton straw pulp products, etc.
(4) According to the color of the raw material (product): natural color (natural color), white, and dyed.
(5) Pulp molding pulp raw materials are divided into biological mechanical pulp, mechanical pulp products, semi chemical mechanical pulp products, chemical mechanical pulp products, chemical pulp products (basically all pulp boards can be made of chemical pulp) and recycled pulp according to the process.
(6) Pulp molding can be divided into non protective products, single protective products (generally waterproof), and dual protective products (waterproof and oil resistant), moisture resistant packaging, anti-static packaging, and high barrier packaging according to their performance.
(7) According to the situation of film covering, it is divided into non film covering products and film covering products (film covering materials include PE/PET/CPET/PP/PBAT/PLA, etc.).
(8) According to printing (or dyeing): color printing (can be divided into monochrome and multicolor; can also be divided into pad printing and screen printing) and non printing, printing ink is divided into water-based ink and industrial ink printing, excluding the dyeing of the entire product.
(9) According to the molding process, pulp molding is divided into grouting type, bailing type, and suction type.
(10) According to the use of steel wire mesh, it can be divided into smooth mesh type and double-sided light type.
(11) Pulp molding equipment types: manual products, semi-automatic machines, and fully automatic machines.